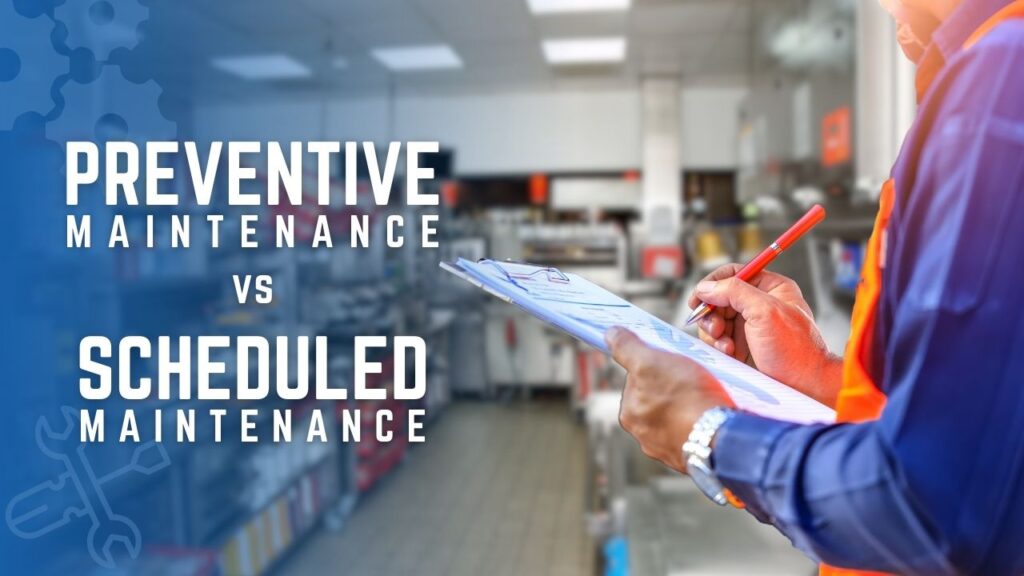
Preventive Maintenance vs. Scheduled Maintenance: Ensuring Equipment Reliability in Restaurants
Maintaining the efficiency and reliability of restaurant equipment is important to keep up with kitchen operations especially during demanding hours. Two common approaches to equipment maintenance are preventive maintenance and scheduled maintenance. While both methods aim to keep restaurant equipment in optimal condition, they differ in their approach and benefits.
Preventive Maintenance
Preventive Maintenance (PM) is a proactive scheduled approach that involves regular annual and sometimes quarterly inspections, adjustments, and cleaning tasks to identify and address potential issues before they escalate into major problems. Its primary purpose is to prevent equipment breakdowns, extend the lifespan of a restaurant equipment, and minimize unexpected downtimes.
Benefits of a Preventive Maintenance
1. Quarterly/Yearly Approach
A preventive maintenance program can be planned quarterly, semi-yearly, or yearly and is generally done on a single specific piece of equipment. It takes a proactive approach by checking all primary systems in the unit and replacing wear items such as belts gaskets and filters. If any issues are identified and work order is created to solve the issue while on site or a return service call can be scheduled to repair the identified issue. By addressing minor issues early on we can limit costly breakdowns and repairs and the challenges with equipment being down. By identifying and addressing minor issues in a timely manner, preventive maintenance saves money by reducing repair expenses and optimizing the lifespan of your equipment.
2. Focuses on Specific Equipment
PM programs are generally done on high importance equipment such as fryers, combi ovens, clamshell grills, refrigeration and “mission critical” kitchen equipment. By focusing on a specific piece of equipment, preventive maintenance ensures that each piece receives the necessary attention, addressing potential risks. This targeted approach in preventive maintenance helps maximize the effectiveness of maintenance efforts, reduces the chances of overlooked or neglected equipment, and ensures that repairs and inspections are conducted at least once a year.
Scheduled Maintenance
Scheduled maintenance (SM) involves performing maintenance activities at predetermined intervals, regardless of the equipment’s current condition. Scheduled maintenance focuses on more of the entire kitchen, not just one specific piece of equipment. This type of maintenance can be scheduled for an entire 12 months and focuses on several pieces of equipment in the restaurant. The primary purpose of scheduled maintenance is to ensure routine tasks are consistently carried out to maintain equipment performance, compliance, and safety. Scheduled maintenances are great for high-demand and busy kitchens to ensure that every piece of equipment is running as expected and delivers consistent results for every use.
Benefits of a Scheduled Maintenance
1. Time-based Approach
A scheduled maintenance relies of a fixed timetable rather than the actual condition of the equipment. This means that maintenance tasks are performed at predetermined intervals regardless of whether the equipment is currently experiencing issue. Similar to a vehicle having set service checks every 5000-6000 miles, this type of maintenance provides a structured approach to equipment care, allowing restaurants to allocate resources, plan workflows, and ensure that maintenance tasks are consistently performed.
Each SM plan is built to the unique specifications and agreement with the owner for the equipment in their kitchen. These programs are highly customizable based on the specific need of the customer and each scope of work is unique based on the customer’s needs.
2. Standardized Tasks on Several Restaurant Equipment
Standardizing maintenance activities simplifies planning and ensures consistent care for all equipment in the kitchen. It streamlines maintenance by having standardized tasks for each equipment type. This approach prevents oversight and guarantees a consistent level of care. It enhances efficiency, reliability, and safety in operations. Ultimately, its goal is to support optimal kitchen performance and ensure that the restaurant delivers consistent results every time.
While both types of restaurant kitchen maintenance focus on the overall reliability of a kitchen equipment, the key differences between preventive maintenance and scheduled maintenance lies in their frequency, focus, and scope. Preventive maintenance is performed quarterly/semi-annually/annually and is focused on a specific piece of equipment. Scheduled maintenance operates on shorter intervals between 60 to 90 days, covers a broader range of equipment, and is customizable to your specific equipment and needs. Both strategies play essential roles in maintaining equipment reliability, longevity, and operational efficiency.
If you’re running a busy kitchen and need to keep up with the demands of your customers, then it might be time to plan a meeting with one of our qualified service sales consultants. There is no obligation, and we can identify what your specific needs are and recommend the plan that fits your business the best.
For busy kitchens in the Northwest, our team of expert technicians and service sales consultants at DSL Northwest can provide you with plans for either preventive maintenance or scheduled maintenance. You may call us at 877-665-1125 or email us at sales@dsl-nw.com.
Comments are closed.